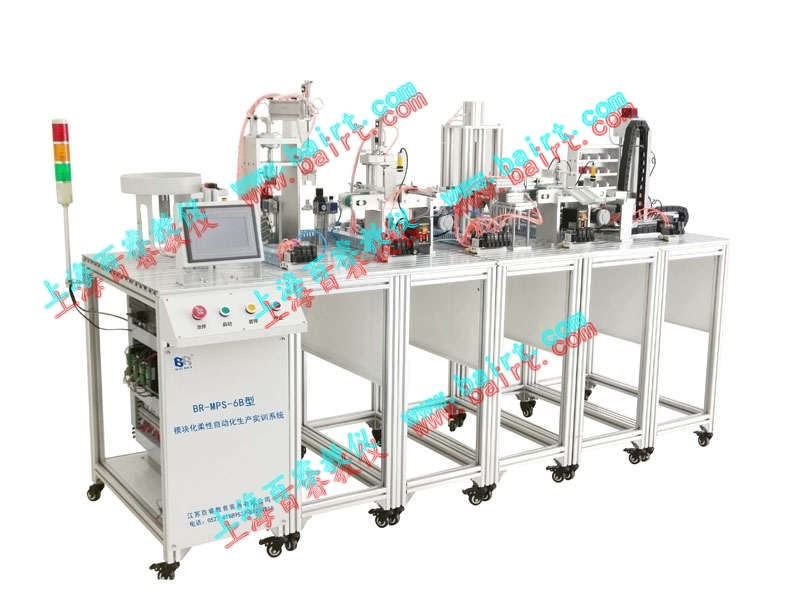
The BR-MPS-6B modular flexible automation production training system has been reduced based on the BR-MPS-8B, with as many as 6 workstations, meeting the teaching requirements of general automation majors for automation control. The BR-MPS-6B integrates teaching and training devices for complex control processes widely used in actual industrial production, and is specially designed according to the development and future trends of modern production logistics systems. It aims to cultivate students' professional knowledge application ability The main goals are comprehensive practical ability and innovative ability.
The device consists of 6 major workstations, including 1 # loading monitoring station, 2 # loading and handling station, 3 # workpiece assembly station, 4 # automatic stamping station, 5 # material sorting station, and 6 # classification unit. It is an electromechanical integrated production line training and assessment device based on modern industrial equipment. Equipped with human-machine interface synchronous monitoring, it forms an automatic production process from a single site to multiple sites. Each station can operate automatically, with a control voltage of DC24V. The controller is installed at the outer end of the drawer panel, and the state of each controller action can be clearly seen. Electrical components are installed inside the drawer to prevent dust and dirt.
Main performance characteristics:
1. Site modularization: The system consists of 6 sites, with a set of control systems. The controller, actuator components, and drawer are embedded in the drawer, which has a beautiful appearance and is easy to observe, and has good dust resistance.
2. Professional breadth: MPS encompasses various technologies such as motor drive, pneumatic, PLC (programmable controller), sensors, etc. in mechatronics learning, solving the problem of students not being able to operate and train on actual production lines. Teachers can guide students in a series of teaching and training topics from design, assembly, programming, debugging to inspection and maintenance at different levels;
3. Flexibility: The entire system is composed of modular tables, which are easy to install/disassemble and maintain;
4. Safety: The system has various protection functions such as short circuit protection, emergency stop protection, limit protection, intelligent protection, etc., which can ensure personal and equipment safety.
Training content:
The BR-MPS-6B modular flexible automation production training system provides a comprehensive application design teaching and training platform, covering various knowledge such as machine, electricity, and gas integration. The specific content includes:
Training on sensor application technology
The system uses various forms of sensors, including inductive sensors, photoelectric sensors, electromagnetic sensors, capacitive sensors, diffuse reflection sensors, and other types of sensors. Each sensor connection line is marked, numbered, and connected to an open controller in a unified plug type. The operating instructions of different sensors and wiring diagrams are attached. Students can fully grasp the usage methods of various industrial sensors, the working methods of sensors in the system, and the precautions for use.
Pneumatic technology training
The device uses a large number of pneumatic components, including various electronic control pneumatic valves, cylinders, pneumatic grippers, vacuum suction cups, vacuum generators, filtering pressure regulating valves, etc. Students can learn how various pneumatic components and other components work together in coordination. Students can fully grasp the usage methods of various components, understand the working performance of components in the production process, and pay attention to the precautions during use.
PLC technology training
Control unit: The system adopts advanced main control S7-300PLC, human-machine interface, MCGS embedded configuration software, etc., which to a greater extent displays the working status of the industrial site and the development direction of modern manufacturing industry.
★ MCGS embedded configuration software: Administrators can conveniently control the operation, pause, continue, stop, etc. of the entire system through various configuration buttons in the configuration monitoring machine; The working status of each station, as well as the material and color of the workpiece, can also be clearly seen on the monitoring screen.
Electrical control system training
The electronic control part of the system is designed in accordance with industrial standards and customs, and all design drawings and instructions are provided as attachments. Students can learn circuit schematic analysis, PLC I/O address matching, and new device circuit connection design analysis methods on the device based on the design drawings.
Mechanical system installation and debugging training
The system allows each group of students to disassemble and reassemble the mechanical parts as required, and debug them until the system is functioning properly, which greatly helps to improve the hands-on ability of students in school.
Motor drive technology training
There are multiple sets of stepper motors and motor driver systems on the system, including dual axis and single axis modes, as well as various other motors. Each driver is digitally controlled by PLC I/O, allowing students to fully learn the characteristics of various types of drivers for various motors. Each module driver can be tested, and students will be able to fully practice.
Training on system maintenance and fault detection techniques
This part of the training focuses on introducing the content and methods of daily maintenance of mechatronics systems, as well as methods for analyzing and troubleshooting common system faults.
Module Function Introduction:
1. Loading monitoring station
Function Introduction: The main function of the feeding detection unit is to sequentially send workpieces from the feedback feeding platform to the detection station, and detect the presence of workpieces. The feeding detection unit mainly consists of a hopper, a rotary table, a material guide mechanism, a material tray height adjustment mechanism, and a workpiece slide. (Note: This station can be equipped with a touch screen for configuration control)
Components: rotating feeding device, alarm device, air source processing component, electrical control system, etc.
.jpg)
(上料监控站图)
The site can conduct the following experiments:
Practical training on the application of photoelectric sensors; DC Motor Forward and Reverse Control Training
PLC control automatic feeding control practical training; PLC control manual feeding control training;
Electrical Control Training Electrical Wiring Control Training; Module Control PLC Programming Control Training.
Touch Screen Configuration Control Training Touch Screen and PLC Communication Training
Practical training on the application of various functional instructions in controllers
2. Loading and handling station
Function Introduction: The main function of the handling unit is to transport workpieces from the loading unit to the waiting area workstation of the processing unit. The handling unit mainly consists of pen shaped cylinders, parallel gripper cylinders, dual axis cylinders, rotary cylinders, etc.
Components: extension and lifting device, rotating device, pneumatic gripper, electrical control system, etc.
.jpg)
(Diagram of Material Handling Station)
The site can conduct the following experiments:
Automatic start stop control training; Practical training on rotating cylinder control;
Air claw control practical training; Electromagnetic valve application training;
Installation of pneumatic directional control circuit; Installation of pneumatic speed control circuit;
Installation and commissioning of pneumatic systems; Sensor application training;
Electrical control training and electrical wiring control training; Module control PLC programming training.
3. Workpiece assembly station:
Function description: The front station transports materials over → The conveyor belt is driven by a three-phase motor, which drives the workpiece forward → Material inspection
The sensor senses the workpiece → the pushing cylinder pushes the workpiece into the assembly platform → the vacuum suction cup places the absorbed assembly workpiece into the previous workpiece → the pushing cylinder supports the upper assembly workpiece, and the cylinder pushes the dropped assembly workpiece to the assembly platform, while pushing out the assembled components. The lowering cylinder pushes the vacuum suction cup down, and the suction cup sucks the assembly workpiece. The lifting cylinder rises to wait for the next assembly.
Composition modules: conveyor belt device, air source processing component.
.jpg)
(Workpiece workstation diagram)
The site can conduct the following experiments:
Sensor application training;
Practical training on sensor positioning applications; Belt transmission control practical training;
Automatic assembly control training; Pneumatic control training;
Module control PLC programming control practical training; Practical training on the application of vacuum generators.
4. Handling and sorting station:
Function Introduction: The front station photoelectric sensor senses that a component has reached the temporary storage area → the mechanical arm lifts the cylinder, rotates the cylinder to the left to reach the designated position, extends the telescopic cylinder forward, and clamps the component → retracts the telescopic cylinder, extends the positioning cylinder, rotates the rotating cylinder to the center position, moves the telescopic cylinder forward, lowers the lifting cylinder, presses down the riveting cylinder, completes the riveting task, returns the riveting cylinder to its original position → rises the lifting cylinder → retracts the telescopic cylinder, Retract the positioning cylinder, rotate the cylinder and continue to rotate to the right position → lower the lifting cylinder → clamp and lower the component.
Composition modules: press device, robotic arm device, and air source processing component.
.jpg)
(Automatic stamping station diagram)
The site can conduct the following experiments:
Sensor application training; Practical training on robotic arm control;
Practical training on stamping machine application; Pneumatic rotation control training;
Automatic sequential process control training; Pneumatic control training;
Module Control PLC Programming Control Training.
5. Material sorting station:
Function Introduction: This station completes the sorting of workpieces, such as: (red, green, blue, material,...) for a series of sorting, pushes out the set unqualified workpieces, continues to transport the qualified workpieces backward, and temporarily stores them through the round-trip mechanism waiting to enter the next station.
Composition modules: belt conveyor, sorting and pushing device, workpiece detection device, round-trip temporary storage device, and air source processing component.
.jpg)
(Material sorting and temporary storage station diagram)
The site can conduct the following experiments:
Practical training on the application of workpiece material differentiation; PLC Application Instruction Training
Practical training on the application of inductive sensors; Material sorting control practical training;
Belt conveyor control installation; Installation of temporary storage control for workpieces;
Installation and commissioning of pneumatic systems; DC motor control training and other practical training projects.
Module control PLC programming control practical training;
6. Classification unit:
Function Introduction: The function of the classification unit is to classify workpieces by type and push them into the material bin. The main structural components of a classification unit are linear modules, classification silos, etc.
Composition modules: three-dimensional conveying device, three-dimensional warehouse device, workpiece ejection device, detection device, and gas source processing component.
.jpg)
(Vertical Warehouse Station Map)
The site can conduct the following experiments:
Two axis linkage stepper motor control training; Pulse control training;
Hall switch application training; Step by step precision positioning control training;
PLC stepper control practical training; Mechanical assembly/installation and debugging training;
Electrical control training and electrical wiring control training; Practical training on PLC power outage maintenance function
Module Control PLC Programming Control Training.
Technical indicators
Input voltage: 220V/50HZ;
Execution driving voltage: 24V/5A;
Environmental temperature: 0-55 ℃ (working) -20-70 ℃ (storage);
Relative humidity: 35-85% (non condensing);
Grounding: the third type of grounding;
Single station size (mm): 400 × seven hundred and fifty × 800, a total of 8 stations, each with the same size;
Gas source: 0.4Mpa -0.75Mpa;
Working environment: It is prohibited to come into contact with corrosive and flammable gases to prevent conductive dust.