
For other hydraulic test benches, please click on the left!
YD-A industrial hydraulic transmission comprehensive experimental platform (upgraded version with fault diagnosis)
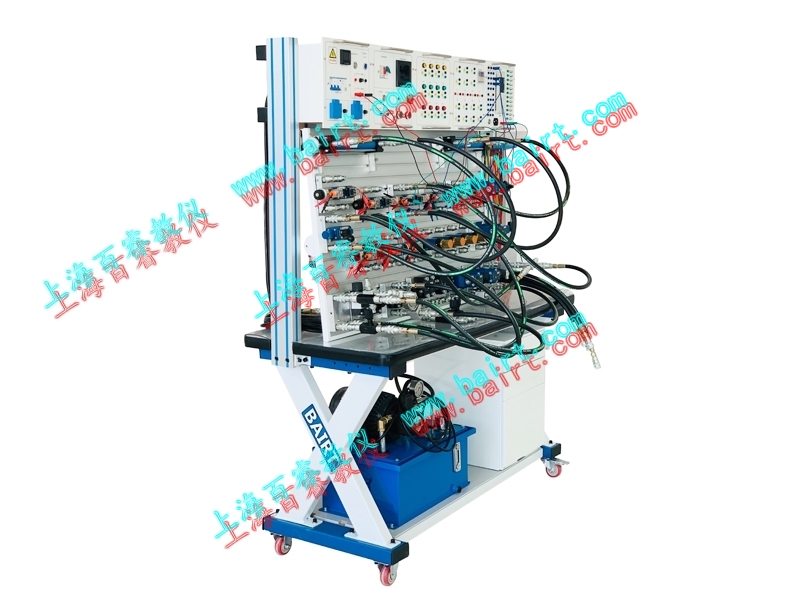
Fashionable profile design
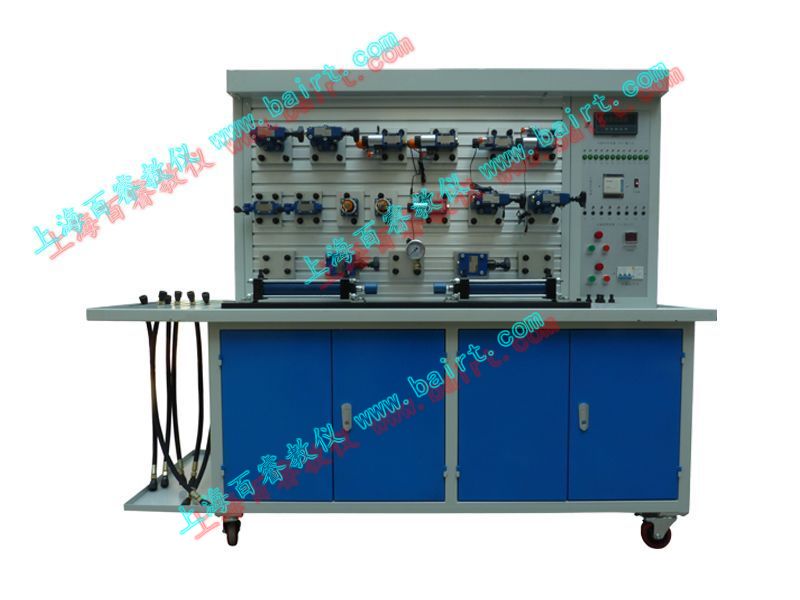
Regular sheet metal models
The YD-A type quick insertion combination hydraulic transmission experimental platform is designed based on modern teaching characteristics and the latest requirements of the hydraulic transmission curriculum teaching outline. It adopts advanced Rexroth technology hydraulic components and unique modularity, forming a convenient system combination that meets the experimental teaching requirements of hydraulic transmission tutorials for students in higher education institutions, secondary professional schools, and vocational and technical schools; The goal is to cultivate students' hands-on, design, and comprehensive application abilities, and to enhance and strengthen their innovative design abilities.
1、 Main features:
1. The system adopts standard industrial hydraulic components, which are safe and reliable to use and close to industrialization.
2. Fast and reliable connection method, special sealing interface, ensuring convenient and fast experimental assembly, no oil leakage during disassembly, and clean.
3. Accurate measuring instruments, convenient measurement methods, simple to use, and precise and reliable measurements.
4. Using programmable logic controllers (PLCs) to communicate with microcomputers, achieving electrical automation control, online programmable monitoring, and fault detection.
5. Add configuration simulation software to enhance functionality.
6. Add hydraulic simulation software, virtual software circuit overlap and fault detection functions.
7. The training, diagnosis, and assessment functions of the experimental platform
System Fault Setting Diagnosis and Troubleshooting Training and Assessment System
This system fault analysis and troubleshooting training and assessment system is an important upgraded and expanded function based on traditional circuit and component testing and data analysis. According to the requirements of national demonstration vocational colleges, it mainly includes component hardware failures, electrical component failures, and electrical system failures. Among them, hardware faults and electrical component faults have independent and identifiable hidden fault codes, making it convenient for teachers to set faults; Electrical system faults can be set through human-machine dialogue, and electrical system troubleshooting is equipped with corresponding exam software, which can test students' troubleshooting ability accordingly.
Parameters and performance
7.1.1. Equipped with a user-friendly human-machine dialogue interface (optional upper computer control)
7.1.2. Customized data analysis control card
7.1.3. Unique assessment system, scientifically rigorous and objective teacher evaluation system
Description and main characteristics of each component
7.2.1. The system data analysis control card can be used for fault expansion, with sufficient expansion interfaces;
7.2.2. The examination system has functions such as system power management, device locking, device unlocking, P-IO, temporary departure, forced collection, score viewing, score export, score printing, clearing scores, and clearing test papers;
7.2.3. The examination software includes two ways to set the assessment mode: manual and random;
7.2.4. Randomly set examination methods can be randomly selected by this software, so as to prevent plagiarism in each assessment;
7.2.5. Power failure protection function to ensure automatic saving of setting data and exam results;
7.2.6. The built-in functions of the software include: querying candidate's relevant data information: number, score, accuracy, unresolved faults, time, and exam status;
7.2.7. Teachers have independent backend passwords to set key data and confirm exam results;
The list of faults that can be manually set is as follows:
7.3.1. The oil pump is working, and there is no pressure in the main circuit
7.3.2. The main relief valve does not overflow
7.3.3. Secondary pressure cannot be formed
7.3.4. Pilot operated relief valve access system, system unloading
7.3.5. The oil cylinder cannot function properly
7.3.6. Various types of solenoid valves cannot operate normally
7.3.7. Manual directional valve stuck
7.3.8. Simulate pump inlet filter blockage
7.3.9 Common faults such as poor sealing of pump inlet pipe and intake of air
7.3.10 Pump Reversal
7.3.11. The outlet of the pressure reducing valve cannot be adjusted to the required pressure
7.3.12. Unidirectional throttle valve unable to adjust flow rate
Students are passively diagnosed, excluded, and teachers take limited time exams to automatically generate grades.
Diagnosis, troubleshooting, and assessment of electrical system faults
7.4.1 Main circuit failure:
The oil pump cannot stop
Emergency stop press cannot stop
The oil pump cannot start
Oil pump jog start
7.4.2 PLC circuit failure:
PLC presses the power switch, PLC has no power (line fault)
PLC power supply has power but no input (input common line fault)
PLC power supply has power but no output (output common line fault)
PLC does not input when pressing the input button (button malfunction)
PLC output has action, panel indicator light does not light up (indicator light malfunction)
Press the proximity switch to activate, but there is no input from the PLC (plug-in failure)
PLC output light on, no output (plugin failure)
7.4.3 Relay module failure
Relay module button fasteners are not responding
The relay module can start but cannot stop
The relay module has no output
There are no external inputs to the relay module
2、 Composition of the experimental platform:
① Experimental workbench
Working power supply: three-phase four wire 380V, rated power: 1.5KW, rated pressure: 6.3-7Mpa
The experimental workbench is composed of an iron body, an electrical cabinet, an oil pipe rack, and an aluminum alloy panel (T-shaped hook groove). Made of high-quality cold-rolled steel plate material with a thickness of 2mm from Baosteel; Beautiful and sturdy, equipped with four high-quality shaft type universal wheels at the bottom, easy to move. The bottom of the cabinet is divided into two parts, with the left side used to place the pump station; On the right is a storage cabinet, used to store hydraulic components.
Workbench
Main size: Long × wide × Height=1500mm × 650mm × 1760mm (approximately 260kg after packaging)
Optional attachment: long × wide × Height=600mm × 650mm (computer comes with approximately 20kg)
Optional fault setting diagnosis training function
Attachment size: 650 × six hundred and fifty × 1500mm
② Hydraulic pump station
Rated working pressure of the system: 6.3Mpa. (Up to 7Mpa maximum)
⑴ Motor pump device (1 unit)
Variable vane pump -1 motor:
Variable vane pump: unidirectional, nominal displacement 6.67mL/r, volumetric efficiency 90%;
Motor: three-phase AC voltage, power 1.5KW, speed 1450r/min;
⑵ Fuel tank: nominal volume 40L; Equipped with liquid level and oil temperature indicators, oil suction filter, air filter, plugs, etc
③ Common hydraulic components
Mainly based on the famous hydraulic brand Beijing Huade components, it works stably and has reliable performance. Please refer to the configuration list for details.
Each hydraulic component is equipped with an oil transition bottom plate, which allows for easy and flexible placement of hydraulic components on aluminum alloy panels.
④ Electrical measurement and control unit
Programmable Logic Controller (PLC): Siemens SMART series, CPU SR20, I/O port 20 points, relay output form; (Customers can choose PLCs with different brand configurations according to their own needs)
Power supply voltage: AC 220V/50Hz, control voltage is DC24V, equipped with manual, automatic, sequential and other control functions
3、 Hydraulic Training Program:
1) Basic hydraulic transmission circuit experiment: 1. Single stage pressure regulating circuit
2. Two stage voltage regulation circuit
3. Pressure reducing circuit of pressure reducing valve
4. Balance circuit of sequence valve
5. Unloading circuit of directional valve
6. Unloading circuit of pilot operated relief valve
7. Pressure maintaining and self-locking circuit of hydraulic control one-way valve
8. Differential circuit
9. Speed switching circuit for short circuiting of speed control valve
10. Throttling valve oil inlet throttling speed control circuit
11. Throttling valve return oil throttling speed control circuit
12. Throttling valve bypass throttling speed control circuit
13. Speed control valve oil inlet throttle speed control circuit
14. Speed control valve return oil throttle speed control circuit
15. Speed control valve bypass throttling speed control circuit
16. Unidirectional synchronous circuit controlled by throttle valve
17. Two position four way electromagnetic directional valve reversing circuit
18. Three position four-way electromagnetic directional valve reversing circuit
19. Two position four-way manual directional valve reversing circuit
20. Sequential valve control sequence action circuit
21. Sequential action circuit controlled by proximity switch
22. Sequential action circuit controlled by pressure relay
2) Programmable Logic Controller (PLC) electrical control experiment, mechatronic and hydraulic integrated control experimental form.
1. Learning PLC instruction programming and ladder diagram programming
2. Learning and Using PLC Programming Software
3. Communication between PLC and computer, online debugging and monitoring
4. Optimization of PLC for Hydraulic Transmission Control
3) Equipped with excavator simulation mechanism (optional) (provide on-site operation video of hydraulic excavator simulation mechanism)
1) Observation, disassembly and assembly of various components in hydraulic transmission, and learning and analysis of hydraulic control system principles.
2) Hydraulic excavator demonstration control experiment.
① Excavation operations, bucket and stick composite work experiments;
② The position and height of the boom can be adjusted simultaneously for unloading operations, bucket operation, and bucket operation.
4) Equipped with loader simulation mechanism (optional) (on-site video of hydraulic loader simulation mechanism operation provided)
1) Observation, disassembly and assembly of various components in hydraulic transmission, and learning and analysis of hydraulic control system principles.
2) Hydraulic loading machinery demonstration control experiment.
① Loading operation, after the bucket is loaded, the rocker arm cylinder extends to reverse the bucket and lift the boom;
② Unloading operation, bucket unloading (rocker arm retracted, causing bucket to turn), boom lowering.
5) Add configuration simulation software to enhance functionality
6) Add hydraulic simulation software, virtual software circuit overlap and fault detection functions.
1. Display the flow direction of hydraulic pressure inside the hydraulic simulation oil pipe;
2. The working indicator light of the electromagnet;
3. Hydraulic cylinder;
4. The structural diagram of a three position four way electromagnetic directional valve, with the valve core capable of switching according to the actual working position;
5. Proximity switch, which can read the working status of the proximity switch in real time; (As shown in the above figure: The green color indicates that the electromagnet is in working condition, and the corresponding PLC port outputs control signals)
6. Hydraulic circuit working principle diagram;
7. Virtual pressure gauge; (You can open the parameter settings on the computer interface to adjust the control pressure of the overflow valve, and display it in the virtual reading of the pressure gauge)
8. Virtual reading of pressure gauge;
9. Quantitative gear pump working part;
10. Hydraulic oil source;
11. Direct acting relief valve;
12. Virtual button control panel, which can replace hardware PLC button signal input;
13. Hydraulic system working status table.
Jiangsu Bairui Education Equipment Co., Ltd. is a production, research and development sales base established and constructed by Shanghai Bairui Education Equipment Group in Suqian City, Jiangsu Province in December 2016. According to the group's requirements, it aims for practical training and is a technology-based enterprise that integrates professional research and development, manufacturing, and sales. Dedicated to the production and sales of specialized products in the fields of intelligent flexible automation, robot cooperation, hydraulic and pneumatic, mold design and manufacturing, mechanical innovation design, and mechanical processing manufacturing in the mechanical majors of undergraduate, vocational, and technician colleges in higher education institutions. Bairui Education Instrument, an enterprise that has obtained national high-tech certification, is located in the dynamic Yangtze River Delta, relying on the Shanghai R&D center. Its production and sales factory is located in Suqian City, Jiangsu Province. It has favorable conditions such as a good investment and financing environment, strong scientific research capabilities, advanced manufacturing technology, strong manufacturing capabilities, convenient transportation, and beautiful ecology. The company covers an area of over 30000 square meters in production and office, with advanced complete processing equipment and complete product testing processes. The company has set up R&D Technology Department, Marketing Department, Work Safety Department, Finance Department, Logistics Supply Department and science and technology research team. The humanized management system is perfect, the supervision mechanism is perfect, and the ISO9001:2015 international quality management system has been operating in a standardized and strict manner for many years. The company has passed the OHSAS18001:2007 occupational health and safety management system certification, ISO14001:2015 environmental management system certification, and passed the GB/T29490-2013 intellectual property management system certification in 2020. It has been rated as: excellent supplier of government procurement, China's independent innovation brand, China's key recommended enterprise in the teaching equipment industry, excellent enterprise in the teaching equipment industry in China, national energy-saving and environmental protection products, and exemplary organization of after-sales service in the education equipment industry for many consecutive years; Obtained AAA level demonstration unit for honest operation, AAA level contract abiding and trustworthy enterprise, AAA level credit rating enterprise, AAA level credit enterprise, National 315 Integrity Enterprise, Top 100 Enterprises in the Industry, National Quality Trustworthy Product, and National Authoritative Testing Quality Qualified Product Certificate. The research team of Jiangsu Bairui Education Instrument has been committed to product improvement and innovation for a long time. They have developed nine series of nearly a hundred stable and advanced science and engineering teaching and training experimental equipment, making our company's basic practical and innovative technology products have a clear advantage in peer competition!